Jagannath Jena, a tribal resident of Alekhapada village in Odisha’s Keonjhar district is rejoiced at being able to support his family by doing something he has always found enjoyable — practising the age-old Dhokra craft.
“Our village is famous for Dhokra craft. This pracheen [ancient] craft has been a source of our livelihood since the time of our ancestors. Now we are back at work after the state government has started organising craft melas [fairs],” the 40-year-old craftsmith told Gaon Connection.
According to Bipin Rout, the joint chief executive officer of Odisha Rural Development And Marketing Society (ORMAS), as many as 5,000 artisans like Jena living in the districts of Cuttack, Dhenkanal, Keonjhar, Angul, Mayurbhanj, Kandhamal , Rayagada, Gajapati, Kalahandi and Koraput are now able to dedicate their traditional skills to produce Dhokra craft which is not only ensuring the preservation of their tribal identity but also helping them earn a livelihood.
Also Read: Dhokra art of Odisha keeps tribal myths and folklore alive in metal
“Odisha is best known for its Dhokra metal casting which is an ancient craft. Decorative as well as utilitarian products like motifs including containers, boxes of different shapes, lamps and lamp stands, table top, etc are amongst some of the excellent specimens of the Dhokra craft produced by these tribal inhabitants,” Rout said.
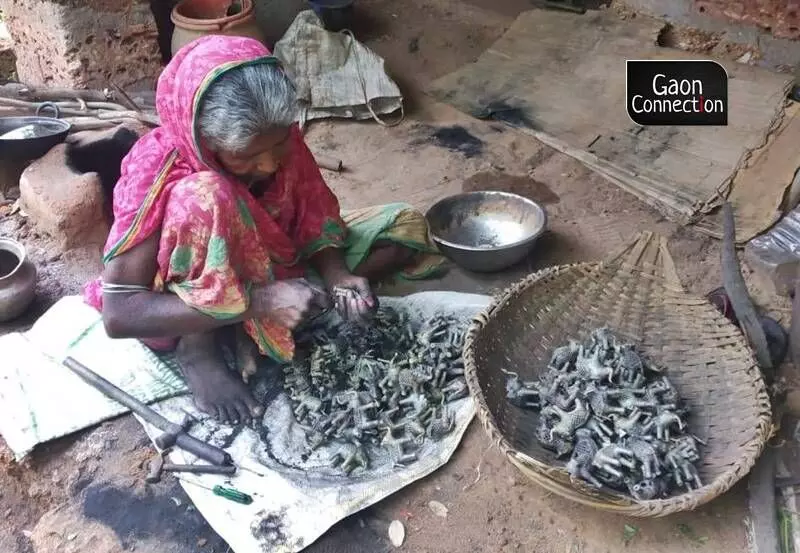
Dhokra craft also involves an elaborate process of creating a mould using clay to create intricate designs and covering it with another layer of river soil. The mould is then placed in an improvised furnace, causing the beeswax to melt and drain away.
The official went on to explain that the economic revival of the Dhokra art was facilitated by the formation of producer groups amongst the artisans and government’s support in providing skill development.
“Also, funds provided by ORMAS for buying the much needed machines and toolkits helped the villagers practise their craft. ORMAS as a facilitating agency also helped in creation of forward linkages to promote marketing of an environmentally friendly product. Their products are appreciated both in national and international markets,” Rout added.
The sale of the Dhokra craft products is conducted mostly at the craft fairs organised by the ORMAS. Also, there is considerable demand for the craft on e-commerce platforms.
Traditional craft helps tribal residents beat pandemic blues
The traumatic experience of losing his job in Mumbai along with the apprehension of losing his life to the COVID-19 outbreak urged Sudam Majhi to find means to earn a living by staying close to his family.
“I have worked as a security guard in Mumbai for many years. But when Corona arrived, I lost my job for which I was living far away from my family. I realised that I need to find some work back home and stay close to my family as life is too unpredictable,” Majhi, a tribal resident of Badabarsingi village in Odisha’s Cuttack district, told Gaon Connection.
Akin to the many self help groups operating at a village level in Odisha’s tribal heartland to promote Dhokra art and ensure a better livelihood for the rural residents, Maa Tarini Self Help Group in Majhi’s village employs a total 30 villagers including Majhi and his wife Kusum — providing sustainable employment and ensuring that the tribal families live together in peace.
“The pandemic created new challenges for us. But now we are busy with our work. I will not leave my village to eke out a living anymore. We are earning around Rs 10,000 from this craft every month, which is far more than what I could send back home while working as a security guard in Mumbai,” Majhi told Gaon Connection.
With hundreds of tribal residents like Majhi having returned to their villages after having quit or losing their jobs in far off cities, the production of the Dhokra art is gradually increasing.
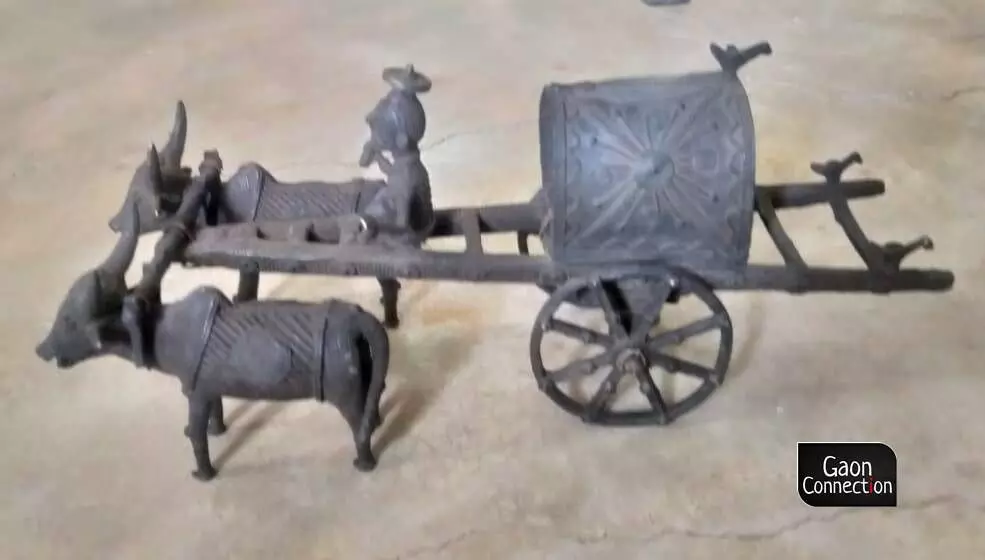
In Dhokra craft, brass is the main metal used to make exquisite products. Other raw materials used in dhokra casting include beeswax (mohum), clay beeswax threads and coal.
Raut, the official working for ORMAS, informed Gaon Connection that almost 70 per cent of the Dhokra craft practitioners are back in their villages from urban areas which has helped in steady rise in the total craft output.
Age-old, sustainable craft using locally available materials
The artisans practising the Dhokra craft follow the traditional method of using wax for metal casting. “I learnt the art of making craft items from my father. We start our work early in the morning as it is not possible to work sitting near the fire while casting metal during the daytime when it gets too hot,” Ajaya Bhuyan, an artisan from Kuliana village in Mayurbhanj district told Gaon Connection.
In Dhokra craft, brass is the main metal used to make exquisite products. Other raw materials used in dhokra casting include beeswax (mohum), clay beeswax threads and coal.
Priya Ranjan Kar, secretary of Odisha Silipi Mahasangha —an organisation of self help groups and artisans making handicrafts in Odisha, informed Gaon Connection that the raw material used is not pure brass but contains miscellaneous scraps of other metals which gives it the typically antique look.
“This ancient craft also involves an elaborate process of creating a mould using clay to create intricate designs and covering it with another layer of river soil. The mould is then placed in an improvised furnace, causing the beeswax to melt and drain away,” she said.
“The mould is then filled with the molten bell metal, and once the mould hardens, it is filled for several hours to reveal the intricate design underneath,” Kar added.